WHAT IS CHEMICAL RECYCLING?
Chemical recycling technologies are designed to convert plastic waste back into raw materials. The process helps accelerate a circular economy for plastics by further increasing and diversifying access to circular feedstock.
Related Content
Chemical producer Dow said March 10 it’s investing in Xycle, a Netherlands-based chemical recycling technology company, to help advance its plastics recycling efforts.
The investment in Xycle is part of Dow’s efforts to transform plastic waste and other forms of alternative feedstocks into 3 million metric tons of circular and renewable solutions annually, said Dow in a press statement. Others joining Dow in the Xycle investment include ING, Invest N-L, Polestar Capital and Vopak.
As part of this effort, the funds will support the construction of Xycle’s first commercial-scale advanced recycling plant, located in the Port of Rotterdam. The facility is expected to be fully operational by the end of 2026, with a projected plastic waste processing capacity of 21 kilotons annually (kta). Dow will use the circular feedstock produced to manufacture new circular plastics.
Dow said Xcycle’s advanced recycling process complements its mechanical recycling solutions, which currently can’t process mixed plastic waste.
Xycle’s advanced recycling technology uses low-temperature pyrolysis to break down mixed plastic waste into pyrolysis oil, increasing the liquid fraction available for use as cracker feedstock in new plastic production. This circular feedstock can be used to manufacture virgin-quality plastics for applications such as food-grade packaging, medical and automotive components.
The modular layout of Xycle’s facilities allows production to scale up or down depending on demand, ensuring both flexibility and efficiency in operations. In the future, Xycle plans to develop more advanced recycling facilities globally, using larger reactor sizes to increase single plant capacity to 100 kta, said Dow.
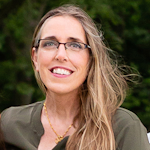
Amanda Joshi | Managing Editor
Amanda Joshi has more than 18 years of experience in business-to-business publishing for both print and digital content. Before joining Chemical Processing, she worked with Manufacturing.net and Electrical Contracting Products. She’s a versatile, award-winning editor with experience in writing and editing technical content, executing marketing strategy, developing new products, attending industry events and developing customer relationships.
Amanda graduated from Northern Illinois University in 2001 with a B.A. in English and has been an English teacher. She lives in the Chicago suburbs with her husband and daughter, and their mini Aussiedoodle, Riley. In her rare spare time, she enjoys reading, tackling DIY projects, and horseback riding.