Understanding Pressure Vessels: Design, Safety and Uses
Key Takeaways for Chemical Engineers
- Pressure Vessel Integrity is Critical – High-pressure differentials, thermal stresses, and external loads make robust design, material selection, and compliance with ASME Section VIII essential to prevent catastrophic failures.
- Advanced Analysis Enhances Safety & Efficiency – Finite Element Analysis (FEA) helps optimize vessel design, ensuring proper stress distribution, minimizing failure risks, and improving long-term reliability.
- Proper Support & Nozzle Placement Reduce Stress Concentrations – Strategic positioning of supports (saddles, skirts, lugs) and nozzles minimizes localized stress points, preventing fatigue and operational failures.
A pressure vessel is a container designed to hold fluids at a pressure differential between its interior and exterior. Common in chemical processing facilities, pressure vessels appear in various configurations including drums, towers, reactors, pressure cookers, autoclaves, retorts and filters.
These vessels facilitate numerous processes, including mixing, filtration and reaction. Some vessels, such as vacuum towers, operate below atmospheric pressure, while others withstand significant positive pressure.
Pressure vessels represent some of the most critical equipment in chemical processing plants. Their typically complex geometry incorporates various structural elements including supports, nozzles and inspection openings. These vessels must maintain integrity under demanding conditions, including high pressures, thermal loads and external forces.
This following is an overview of different types of pressure vessels, design considerations and their uses in chemical processing applications.
Pressure Vessels 101
Pressure vessels usually should withstand a combination of high pressures together with high or low temperatures, wind loads, dynamic loads and others. They should be designed and manufactured carefully to cope with the operating pressure and temperature and all imposed loadings. Another concern is, in many cases, the containing fluid is hazardous or challenging such as it might be flammable, explosive, corrosive or toxic. Because of such hazards and risks, additional requirements, such as “absolutely no leakage,” can be specified and enforced.
The size, geometry, dimensions and configurations of pressure vessels vary greatly from the very large cylindrical vessels used as tall towers or massive reactors to the small-size vessels used for small utility services, such as small filters and separators.
Criticality of Pressure Vessels
High pressures have commonly been used in chemical processing industries. For pressure vessels, such high-pressure differentials have been dangerous and risky. This is even risker and more dangerous when combined with other loadings and effects, such as thermal loadings/effects, wind loads, seismic loads and dynamic loads.
Improper use or design of pressure vessels have led to many fatalities. Consequently, engineering authorities, such as the American Society of Mechanical Engineers (ASME), have regulated design, manufacturing and operation of pressure vessels. This includes ASME Section VIII.
Specifically, the shell or head wall should be thick enough, and the stress level on the shell wall and all other components should be sufficiently low as to avoid failure.
Pressure vessel failures are due to several issues, including faulty design, poor manufacturing, such as welding problems or wrong materials and improper installation. Other causes include fatigue, cracking, leakage, creep or embrittlement. Operator error is another factor contributing to failure, including overpressure and excessively high temperatures, in addition to poor maintenance.
Categories, Types and Function
These are two major categories of pressure vessels: horizontal and vertical. Some pressure vessels have internal components and others do not. The main functions of the ones without internals can be storage (or retention) of a fluid stream for a limited or extended period to provide a phase separation by settling or similar. Their sizes may be established by definite process calculations, sometimes using simulations, or by general rules based on experience. Pressure vessels with internals comprise the shell (or housing) of equipment such as towers, reactors, fractionators and filters. Typically, the housing can be designed and constructed independently of details of internals. Their major dimensions are established by process requirements.
Drums in the form of vertical or horizonal vessels have seen extensive use in many facilities. In a typical plant, drums have a holdup of a few minutes. Surge drums between equipment provide a measure of stability in that fluctuations are not transmitted freely along a processing chain, including operational fluctuations such as those due to normal sensitivity of control instruments.
Design, Considerations, FEM and Optimization
Most pressure vessels are made with cylindrical shells. The heads are nearly always a curved shape. Spherical vessels have a limited process applications. Some codes specify the minimum thicknesses for a vessel shell or head. It’s important to follow these requirements even if an analysis suggests a lower thickness threshold. These mandatory requirements are in place for a reason. For example, some inaccuracies and simplifications exist in commonly used pressure vessel formulations. That’s why some safety margins and additional rules are required. Also, there could be different buckling modes, including various local, plastic and elastic-plastic, for pressure vessels with very thin shells. These buckling modes are not routinely checked in the common pressure vessel design procedures.
Stresses on vessel parts involve many variables and parameters depending upon the size and details of vessel, the pressure, the temperature, the service, the arrangement of the supporting structure, the piping attached to the vessel as installed, such as nozzle loads.
Generally, the Finite Element Method (FEM) should be used to determine stresses and design a pressure vessel. FEM subdivides the pressure vessel into smaller, simpler elements called finite elements, a form of space discretization. Then, governing equations applied to finite elements and results, such as stresses, and strains, are calculated numerically. Nowadays, nearly all medium, large or critical-pressure vessels are analyzed by FEM.
An optimization is nearly always needed to find optimum thickness and other key dimensions. A parametric study of the effects of geometric parameters on the maximum effective stresses would help to find the optimum design.
Pressure Vessel Supports
Pressure vessels need supports in different forms such as saddles for horizontal vessels, brackets or lugs for either vertical or horizontal vessels and straight or flared skirts for towers and other tall vessels. These supports should bear the weight of the vessel and contents and imposed loads including many different loads, such as wind and seismic loads. In other words, all forces acting on a vessel are nearly always transferred to its support.
The presence of supports has two main effects on the pressure vessel. Firstly, it interferes with the normal expansion or contraction of the vessel due to internal pressure or temperature change, as an example. Secondly, the concentrated support reaction induces highly localized stresses in the support region. In other words, there are zones of high localized stresses at the junction part of the pressure vessel and supports.
The support structure itself is also stressed. Any support needs a very careful design and configuration. The design of support for pressure vessels is an important part of pressure vessel design task. The main cause of stress concentration is the abrupt transition of structural rigidity between the vessel and the support (or the nozzle).
In successful support or saddle designs, the main plates should be selected with optimum thickness and gusset plates have used for strength to resist different modes of buckling and to bear complicated set of forces/moments due to different effects (generally 3D in nature).
Nozzles and Opening
Various nozzles and openings are required in pressure vessels to allow for different functions. These include inlet, outlet and instrument connections, among others. Openings, such as inspection nozzles and manholes, are required to allow inspection of internal or access to the internal part of the vessel. The size and disposition of the openings depend upon the duty and size of the vessel. Access is absolutely necessary for the installation of internals for pressure vessels with internals.
In a small pressure vessel, a single handhole or a flanged-in inspection opening may be adequate, whereas large vessels require several large access manholes, often with reinforcements or seating rings. Many different designs and configurations exist for such manholes and openings. They can be on the head, side or top of the pressure vessel. Alternatively, heads may be flanged inward (reverse knuckle) to provide a seating surface.
On one hand, the number of nozzles and opening should be kept to a minimum because they are potential leakage points and sources of stress. They are difficult, expansive and time-consuming to design, manufacture and maintain. On the other hand, nozzles and openings as required by the process and operation should be considered for any pressure vessel to function properly.
It is theoretically possible to relocate nozzles and redesign or relocate supports to change the stresses developed in the shell or head of a pressure vessel.
Saddle Supports of Horizontal Pressure Vessels
Horizontal pressure vessels are usually supported on two vertical cradles called saddles. The saddle supporting plays an important role in the design, performance, and reliability of horizontal vessels. The use of more than two saddles is unnecessary and should be avoided, although three saddles (or more) were used in some traditional and old-fashioned long horizontal vessels.
There have been reasons behind the two-saddle practice. One is to avoid an indeterminate structure, both theoretically and practically. With two saddles, there is a high tolerance for soil or foundation settlement with no significant change in shell stresses or loading. Even where settlement is not an issue, it’s difficult to ensure that the loads and stresses are uniformly distributed when more than two saddles are used.
A more rigid support will give rise to greater stress concentration compared to a more flexible one. The use of high stiffness supports, like massive concrete saddles, is unfavorable considering the strength of the pressure vessel.
A rule of thumb, based on bending mode of the vessel, suggests that the supports should be located at 0.21–0.23 of the vessel-length from the ends. However, there have been other suggestions, which consider possible distortion that may occur when concentrated loads are applied to the relatively thin shell of a pressure vessel. To lessen this effect, supports are recommended to be located relatively close to “Diameter/4” from the ends to take advantage of the stiffening effect of the heads.
The selection of saddle diameter also affects the stresses in the pressure vessel. Typically, such diameter is 1% to 2% larger than vessel diameter. The saddle support with extended top plate can reduce the peak stress at the support and also stresses at the shell of the pressure vessel. As a rough indication, an extension of the saddle plate by 10° can cause a stress reduction of 20%–25% in both vessel and support. Therefore, wide saddle support with coverage of more than 140°, as close as possible to 160°, is preferred.
Pressure vessels remain indispensable components in chemical processing facilities, requiring meticulous design, manufacturing, and maintenance to ensure safe and reliable operation. As technology advances, ongoing research and development in materials, design methodologies, and analysis techniques will continue to enhance the efficiency, safety and longevity of these critical industrial components. ⊕
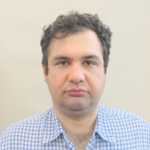
Amin Almasi | rotating equipment consultant
AMIN ALMASI is a mechanical consultant based in Sydney, Australia. He specializes in mechanical equipment and offers his insight on a variety of topics including pumps, condition monitoring, reliability, as well as powder and fluid handling and water treatment.