Barry on Batteries: Inside the Quality Control Lab of Lithium-Ion Cell Manufacturing
Three Key Takeaways
- Lithium-ion battery quality control (QC) shares parallels with pharmaceutical and specialty chemical manufacturing. The stringent QC standards and complex manufacturing steps required for battery production call for similarly thorough materials testing, contamination control and precision requirements.
- Lithium-ion battery testing involves an electrical component check as well as consideration of air handling, metal fines, corrosion and more contamination and safety risks.
- This rapidly evolving and critical technological field presents a growth area for professionals experienced in QC and manufacturing processes. Gaining expertise in cutting-edge tools like X-ray/CT imaging, high-potential testing and materials recycling will help at each step of the process.
In the previous column, we discussed the complexity of lithium-ion battery cell manufacturing, beginning with the cathode active material (CAM), anode material, separators and electrolytes through the final module assembly.
We also explored how the quality standards for these cells compare to those required for active pharmaceutical ingredients (APIs) or specialty chemicals. With 11 steps and sub-steps in cell manufacturing, once again, we need to view “think like a chemical plant.”
As in APIs or specialty chemical manufacturing, the incoming material quality control, or IMQC, for cells is equally critical. In the slurry mixing step, the cathode and anode slurries are formed. This entails mixing powders and liquid solvents. Before testing, cell manufacturers must determine the powder specifications, including particle size distribution, shape, densities, porosity and specific surface area.
In addition, manufacturers must determine acceptable contamination thresholds (for example, 20 ppm–150 ppm for iron levels).
As for the final slurries, an important parameter is the slurry viscosity, which determines the coating efficiencies onto the foils and the thickness of the coating itself. If all of this sounds familiar, these are the normal and standard concerns in a chemical quality control lab.
I must bring up one more point before we leave this step. Solid-liquid filtration engineers will also examine particle interactions or Zeta Potential. In this slurry mixing step, the particle Zeta Potential will influence the lithium-ion diffusion rate and impact cell performance.
Foil Production and Quality Inspection
As we move on to the foils manufacturing process, we encounter drying, calendaring, slitting and notching and stacking and winding steps. The main testing in this phase is visual inspections with camera systems and charged-coupled devices.
These systems will detect whether the batteries are correctly placed in series-parallel positive and negative electrodes and detect spot welding defects. X-ray machines and CT scanning can also help identify welding defects, electrode alignment, material integrity and stacking/layering quality.
Hipot, or high-potential, testing also is necessary at this stage to measure a battery's insulation and ability to withstand voltage surges. The final quality checks include helium leakage tests and moisture tests after final drying and welding. Any defective cells can be removed from the production line and classified as “dry scrap,” as the electrolyte has not yet been introduced into the cell. These cells must be recycled in a separate facility as they contain the CAM and anode materials.
Before we continue, let’s look back at the IMQC for the mechanical components. These include the actual cap assemblies, separators and current interruption disks. As with quality control protocols for manufacturing chemical pressure vessels, material specifications are required. With vessels, for example, material QC ensures that the stated material is correct. It’s important to also check the battery components for materials of construction, smoothness/roundness and burrs.
We are now ready to fill the cells with electrolyte to begin the cell assembly process. This testing involves weighing the empty and filled cells as well as leak testing. Once formation and aging begins, the cells must be checked for charging and discharging times, quality for capacity, voltage and cycle life. The cells then go through final laser welding and cleaning. Cells that are defective at this point are called “wet scrap” as they contain electrolyte as well as the CAM and anode materials. As above, these cells must also be recycled.
The Final Test
The entire process then concludes with open-circuit voltage testing to measure the battery’s voltage and internal resistance before shipping. These tests correct for temperature variations and require idle time before testing. There may be several rounds of this testing with different idle times that can range, for example, from 2–72 hours.
Well, what do you think about lithium-ion battery quality testing versus APIs or chemicals? Battery QC testing appears to be at least as rigorous as chemical/API testing protocols and potentially more advanced given the additional electrical component verification that isn't typically required in chemical or API operations.
We also did not consider contamination mitigation in air handling, metal fines from mechanical operation, corrosion and similar issues facing chemical plants. These additional challenges further highlight the complex quality control demands in battery manufacturing. Quality control experts from the chemical and pharmaceutical industries will find their skills highly transferable, with abundant opportunities to apply their expertise in the rapidly expanding lithium-ion battery cell manufacturing market.
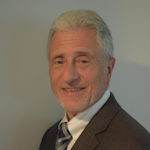
Barry Perlmutter | President of Perlmutter & Idea Development (P&ID) LLC
Barry Perlmutter is president of Perlmutter & Idea Development (P&ID) LLC. He has over 40 years of science, engineering and business marketing experience in the field of solid-liquid separation including filtration, centrifugation, process drying, mixing and recycling. His strong professional skills focus on process and project solutions, innovation strategies and execution, market expansion and business development. Barry has published and presented worldwide on applications in the chemical, pharmaceutical, and energy/environmental industries and has been responsible for introducing many European technologies into the Americas marketplace. His two books, published by Elsevier, Amsterdam, "Handbook of Solid-Liquid Filtration" and "Integration & Optimization of Unit Operations" are used worldwide for process guidance.